Interesting article that showed up in Stereophile magazine email yesterday...
Farewell to the Paper Cone
Irving M. Fried | Jun 6, 2019 | First Published: Sep 1, 1962
https://www.stereophile.com/content/farewell-paper-cone
Ever since the first electrical loudspeaker?a glorified headphone with a horn on it?was outmoded by the balanced-armature cone speaker, paper has been the standard diaphragm material for speakers reproducing low frequencies. The Rice-Kellogg moving-coil transducer replaced the balanced-armature driving system in 1925, but the paper cone remained. And although many improvements have since been made, were no more major changes in loudspeaker design for over 30 years!
Paper was cheap and readily available, and when properly baffled in a large horn or bass-reflex enclosure, to minimize its excursions (by maintaining efficient coupling to the air) and damp out its bass resonance, the paper cone seemed to be the ideal woofer diaphragm. But this was only because it had never been compared with anything better.
When Britain's Peter Walker demonstrated the first full-range electrostatic speaker system in 1955, the paper-cone systems sounded so muddy by comparison that dynamic-speaker designers scurried back to their labs to try to build dynamics that sounded like electrostatics.
They might have had some success, too, had not stereo created a demand for compactness in speakers. The small enclosure aggravated every problem that had existed in large enclosures, so instead of being able to improve the dynamic-speaker sound of the big systems, designers were hard put to equal it from a small box.
The effectiveness of the moving-coil loudspeaker depends on its diaphragm's ability to follow the motions of its voice-coil. The ideal diaphragm behaves like a piston, whose surface moves as a unified plane in accordance with the voice-coil's movements. Any cone motions that do not coincide with voice-coil motions represent distortion, and this is paper's major weakness.
A paper cone is inherently flexible, so the only part of it that follows precisely the motions of the voice-coil is that immediately surrounding the voice-coil. Beyond this small area, flexure of the cone absorbs increasing amounts of vibrations until, at the rim, much of the original vibratory motion has been lost. And because of this lack of control over the whole cone surface, large areas of the cone are left free to break into spurious vibrations on their own at certain frequencies.
Stroboscopic studies of cones in motion have shown that this breakup occurs at various frequencies throughout the speaker's entire range, and becomes worse as vibration amplitudes increase. It is particularly severe at low frequencies, where the cone must travel appreciable distances.
This is why small enclosures cause so much trouble. Without the efficient bass coupling of a more ideal enclosure, the speaker must be made to yield increasing excursions with diminishing frequency, to retain full bass response. This means its excursions in the bass range must be at least twice as great as they would otherwise be, and this in itself aggravates the normal flexing of the paper.
Some manufacturers, questioned about the boxiness, bass deficiency, and lack of clarity in their small speaker systems, tried to talk themselves out of the dilemma, claiming that those little problems really weren't problems at all?stereo would restore the lost clarity and bass, and the boxiness was just a matter of personal opinion. Others, hoping to retain at least some of the quality standards that had been set by the mammoth horns and reflex systems, had to make some drastic changes in their speaker designs.
Various stuffing materials were used to eliminate the boxy sound of the small enclosure, but these caused some problems of their own, by absorbing certain frequencies more readily than others.
In attempting to ameliorate the cone breakup problem, designers tried stiffer cones, made of heavier paper, but these reduced the system's efficiency as well as the woofer's upper frequency response. The choice then was between ignoring the resulting midrange hole, or trying to design a crossover system to work in the region where their design problems are greatest (the 400?2000Hz range).
Variable-density cones?heavy and rigid near the voice-coil, and tapering to thin and light at the rim?were tried in an effort to combine the advantages of lightness and stiffness, but they suffered from the disadvantages of both. Their upper-range response was poor, and they, too, failed to operate like the ideal piston radiator.
Polymerized paper, light in weight but stiffened with a plastic impregnation, was a step in the right direction, but it tended to ring at certain frequencies, coloring the sound.
Impregnated linen cones with corrugations or spiral compliance rings, cambric cones with "dimples" on them, and thin metal-foil cones all showed some promise, particularly the metal-foil design, but the best of them were prohibitively expensive.
One of the most successful papercone variants was the brain child of Arthur Janszen, who needed a woofer to complement his electrostatic tweeter. Instead of thickening the cone paper, he reinforced it with a large conical "plug" of light, rigid polyurethane plastic. The woofer came closer to matching the electrostatic's clarity than had anything before it, and is still used with Janszen-designed electrostatic tweeters in systems made by Neshaminy Electronic Co.
Another engineer named Paul DeMars attached a foam plastic extension to a standard paper-cone woofer, to yield a 30" job whose main shortcoming was its lack of consumer enthusiasm.
Research into the full possibilities of other cone materials was not, however, the kind of project that the average speaker manufacturer could undertake. Most of them had been buying their cones and magnets ready-made for assembly, from the few suppliers of such items in the USA and Great Britain. So the initial research into new cone materials was done by the large speaker manufacturing outfits.
By late 1961, Electro-Voice was ready to announce a 30" woofer incorporating a radically new cone material: polystyrene foam. Almost simultaneously, Jensen unveiled their "Polytec" speakers, also with expanded (foam) polystyrene cones. Meanwhile, two British firms were announcing the fruits of their efforts along similar lines. Leak with a "sandwich" speaker, and Rola Celestion with their "Colaudio" speaker. Other designs followed.
In England, reviewers were highly enthusiastic about the new speakers, but the "official" US reaction has been more tentatively favorable, perhaps because our audio press doesn't understand just what the new cone material does for the dynamic speaker.
All the designers are working with the same material: some form of expanded polystyrene. It is available in a wide variety of densities and textures, it does not absorb water in damp weather (as does paper), it does not dry out and become brittle, and it is chemically very stable. It can be molded, turned, or formed into practically any shape, and it can be chemically treated during manufacture to provide virtually any frequency or damping characteristic. But its most attractive feature is that it can be made far more rigid than the same weight of paper. Hence, it can be both lightweight and stiff, to yield much better piston action than the best of the paper cones.
Let's look at some of its currently available forms. Electro-Voice's 30" woofer has the standard cone shape. The Jensen Polytec woofer uses a hollow "cantilever" plug, with a shallow conical rear and a flat front surface that is driven from around its edge. Jensen's tweeter has a polytec cone of fairly conventional shape, while the supertweeter has a convex dome-shaped diaphragm that is driven from its outer edge. The British IMF styrene woofer's radiator is conical at the rear, convex and dome-shaped in front, and of solid foam all the way through. The Leak "sandwich" is conventional in shape, but its cone is of 3/8"-thick styrene foam covered with duraluminum foil. The British KEF woofer (soon to be available here), and the GE-GO Orthophase speaker are "sandwich" systems?flat on both sides, and driven over their entire front surface by a system of duraluminum ribbons.
All polystyrene speakers do not sound alike, but they do share a certain clarity and freedom from the turgid, mushy coloration of the small-box wide-range paper-cone systems. Indeed, they sound much more like electrostatics than do conventional dynamics, and have a quality of crispness that we used to associate only with the large horn or reflex-loaded systems. The reason is obvious: the electrical energy is being used for sound production, rather than for cone flexing.
An A-B comparison with a paper-cone speaker reveals another interesting difference: the polystyrene's superior rigidity and lower mass allow it to reproduce more of the program's dynamic range, because so much less of the voice-coil's movement is lost in flexure of the polystyrene cone.
Are polystyrenes here? Definitely. However, as is true of electrostatics, the good ones are expensive. There are still some design and production problems that must be ironed out before they can be made well and cheaply, but as the techniques are perfected, we can safely predict that all high-quality loudspeakers will eventually abandon the venerable, obsolete paper cone.?Irving Fried
Footnote: Irving M. Fried (as in Siegfried), a Harvard law school grad and practicing "part-time" lawyer, owns and operates Lectronics of City Line Center, in peripheral Philadelphia. Besides importing British audio components and selling custom installations, Mr. Fried also finds time to write numerous articles for the hi-fi magazines and, more recently, for his own Lectronics Newsletter. Mr. Fried confesses to at least partial responsibility for the development of the Klipsch and Lowther horns and the AR-Janszen combination, and for the introduction of the Janszen electrostatic tweeter. He was the first US importer of the Quad full-range electrostatic, and is currently doing consulting work in the development of new loudspeakers in Great Britain.
?J. Gordon Holt
NEXT: Pro and Con the Paper Cone ? https://www.stereophile.com/content/farewell-paper-cone-pro-and-con-paper-cone
Farewell to the Paper Cone
Irving M. Fried | Jun 6, 2019 | First Published: Sep 1, 1962
https://www.stereophile.com/content/farewell-paper-cone
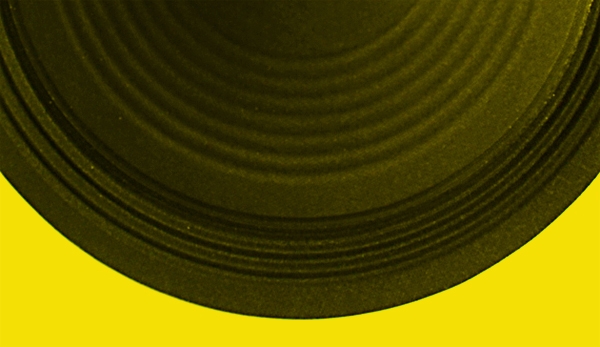
Ever since the first electrical loudspeaker?a glorified headphone with a horn on it?was outmoded by the balanced-armature cone speaker, paper has been the standard diaphragm material for speakers reproducing low frequencies. The Rice-Kellogg moving-coil transducer replaced the balanced-armature driving system in 1925, but the paper cone remained. And although many improvements have since been made, were no more major changes in loudspeaker design for over 30 years!
Paper was cheap and readily available, and when properly baffled in a large horn or bass-reflex enclosure, to minimize its excursions (by maintaining efficient coupling to the air) and damp out its bass resonance, the paper cone seemed to be the ideal woofer diaphragm. But this was only because it had never been compared with anything better.
When Britain's Peter Walker demonstrated the first full-range electrostatic speaker system in 1955, the paper-cone systems sounded so muddy by comparison that dynamic-speaker designers scurried back to their labs to try to build dynamics that sounded like electrostatics.
They might have had some success, too, had not stereo created a demand for compactness in speakers. The small enclosure aggravated every problem that had existed in large enclosures, so instead of being able to improve the dynamic-speaker sound of the big systems, designers were hard put to equal it from a small box.
The effectiveness of the moving-coil loudspeaker depends on its diaphragm's ability to follow the motions of its voice-coil. The ideal diaphragm behaves like a piston, whose surface moves as a unified plane in accordance with the voice-coil's movements. Any cone motions that do not coincide with voice-coil motions represent distortion, and this is paper's major weakness.
A paper cone is inherently flexible, so the only part of it that follows precisely the motions of the voice-coil is that immediately surrounding the voice-coil. Beyond this small area, flexure of the cone absorbs increasing amounts of vibrations until, at the rim, much of the original vibratory motion has been lost. And because of this lack of control over the whole cone surface, large areas of the cone are left free to break into spurious vibrations on their own at certain frequencies.
Stroboscopic studies of cones in motion have shown that this breakup occurs at various frequencies throughout the speaker's entire range, and becomes worse as vibration amplitudes increase. It is particularly severe at low frequencies, where the cone must travel appreciable distances.
This is why small enclosures cause so much trouble. Without the efficient bass coupling of a more ideal enclosure, the speaker must be made to yield increasing excursions with diminishing frequency, to retain full bass response. This means its excursions in the bass range must be at least twice as great as they would otherwise be, and this in itself aggravates the normal flexing of the paper.
Some manufacturers, questioned about the boxiness, bass deficiency, and lack of clarity in their small speaker systems, tried to talk themselves out of the dilemma, claiming that those little problems really weren't problems at all?stereo would restore the lost clarity and bass, and the boxiness was just a matter of personal opinion. Others, hoping to retain at least some of the quality standards that had been set by the mammoth horns and reflex systems, had to make some drastic changes in their speaker designs.
Various stuffing materials were used to eliminate the boxy sound of the small enclosure, but these caused some problems of their own, by absorbing certain frequencies more readily than others.
In attempting to ameliorate the cone breakup problem, designers tried stiffer cones, made of heavier paper, but these reduced the system's efficiency as well as the woofer's upper frequency response. The choice then was between ignoring the resulting midrange hole, or trying to design a crossover system to work in the region where their design problems are greatest (the 400?2000Hz range).
Variable-density cones?heavy and rigid near the voice-coil, and tapering to thin and light at the rim?were tried in an effort to combine the advantages of lightness and stiffness, but they suffered from the disadvantages of both. Their upper-range response was poor, and they, too, failed to operate like the ideal piston radiator.
Polymerized paper, light in weight but stiffened with a plastic impregnation, was a step in the right direction, but it tended to ring at certain frequencies, coloring the sound.
Impregnated linen cones with corrugations or spiral compliance rings, cambric cones with "dimples" on them, and thin metal-foil cones all showed some promise, particularly the metal-foil design, but the best of them were prohibitively expensive.
One of the most successful papercone variants was the brain child of Arthur Janszen, who needed a woofer to complement his electrostatic tweeter. Instead of thickening the cone paper, he reinforced it with a large conical "plug" of light, rigid polyurethane plastic. The woofer came closer to matching the electrostatic's clarity than had anything before it, and is still used with Janszen-designed electrostatic tweeters in systems made by Neshaminy Electronic Co.
Another engineer named Paul DeMars attached a foam plastic extension to a standard paper-cone woofer, to yield a 30" job whose main shortcoming was its lack of consumer enthusiasm.
Research into the full possibilities of other cone materials was not, however, the kind of project that the average speaker manufacturer could undertake. Most of them had been buying their cones and magnets ready-made for assembly, from the few suppliers of such items in the USA and Great Britain. So the initial research into new cone materials was done by the large speaker manufacturing outfits.
By late 1961, Electro-Voice was ready to announce a 30" woofer incorporating a radically new cone material: polystyrene foam. Almost simultaneously, Jensen unveiled their "Polytec" speakers, also with expanded (foam) polystyrene cones. Meanwhile, two British firms were announcing the fruits of their efforts along similar lines. Leak with a "sandwich" speaker, and Rola Celestion with their "Colaudio" speaker. Other designs followed.
In England, reviewers were highly enthusiastic about the new speakers, but the "official" US reaction has been more tentatively favorable, perhaps because our audio press doesn't understand just what the new cone material does for the dynamic speaker.
All the designers are working with the same material: some form of expanded polystyrene. It is available in a wide variety of densities and textures, it does not absorb water in damp weather (as does paper), it does not dry out and become brittle, and it is chemically very stable. It can be molded, turned, or formed into practically any shape, and it can be chemically treated during manufacture to provide virtually any frequency or damping characteristic. But its most attractive feature is that it can be made far more rigid than the same weight of paper. Hence, it can be both lightweight and stiff, to yield much better piston action than the best of the paper cones.
Let's look at some of its currently available forms. Electro-Voice's 30" woofer has the standard cone shape. The Jensen Polytec woofer uses a hollow "cantilever" plug, with a shallow conical rear and a flat front surface that is driven from around its edge. Jensen's tweeter has a polytec cone of fairly conventional shape, while the supertweeter has a convex dome-shaped diaphragm that is driven from its outer edge. The British IMF styrene woofer's radiator is conical at the rear, convex and dome-shaped in front, and of solid foam all the way through. The Leak "sandwich" is conventional in shape, but its cone is of 3/8"-thick styrene foam covered with duraluminum foil. The British KEF woofer (soon to be available here), and the GE-GO Orthophase speaker are "sandwich" systems?flat on both sides, and driven over their entire front surface by a system of duraluminum ribbons.
All polystyrene speakers do not sound alike, but they do share a certain clarity and freedom from the turgid, mushy coloration of the small-box wide-range paper-cone systems. Indeed, they sound much more like electrostatics than do conventional dynamics, and have a quality of crispness that we used to associate only with the large horn or reflex-loaded systems. The reason is obvious: the electrical energy is being used for sound production, rather than for cone flexing.
An A-B comparison with a paper-cone speaker reveals another interesting difference: the polystyrene's superior rigidity and lower mass allow it to reproduce more of the program's dynamic range, because so much less of the voice-coil's movement is lost in flexure of the polystyrene cone.
Are polystyrenes here? Definitely. However, as is true of electrostatics, the good ones are expensive. There are still some design and production problems that must be ironed out before they can be made well and cheaply, but as the techniques are perfected, we can safely predict that all high-quality loudspeakers will eventually abandon the venerable, obsolete paper cone.?Irving Fried
Footnote: Irving M. Fried (as in Siegfried), a Harvard law school grad and practicing "part-time" lawyer, owns and operates Lectronics of City Line Center, in peripheral Philadelphia. Besides importing British audio components and selling custom installations, Mr. Fried also finds time to write numerous articles for the hi-fi magazines and, more recently, for his own Lectronics Newsletter. Mr. Fried confesses to at least partial responsibility for the development of the Klipsch and Lowther horns and the AR-Janszen combination, and for the introduction of the Janszen electrostatic tweeter. He was the first US importer of the Quad full-range electrostatic, and is currently doing consulting work in the development of new loudspeakers in Great Britain.
?J. Gordon Holt
NEXT: Pro and Con the Paper Cone ? https://www.stereophile.com/content/farewell-paper-cone-pro-and-con-paper-cone